HandiCREA e Fondazione habitat umano, insieme per costruire ambienti di vita accessibili
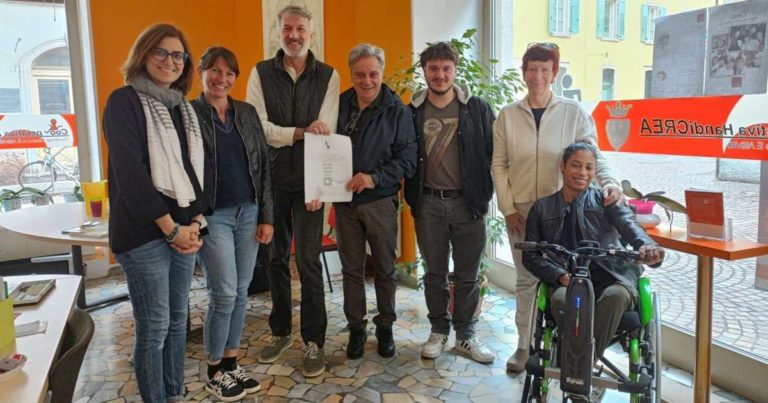
Nasce una collaborazione strutturata tra la cooperativa di Trento fondata da Graziella Anesi e la Fondazione di Lipari guidata dall’architetto Francesco Ferrara per promuovere il diritto alla piena partecipazione delle persone con disabilità nei territori e negli spazi di vita…